Logistics
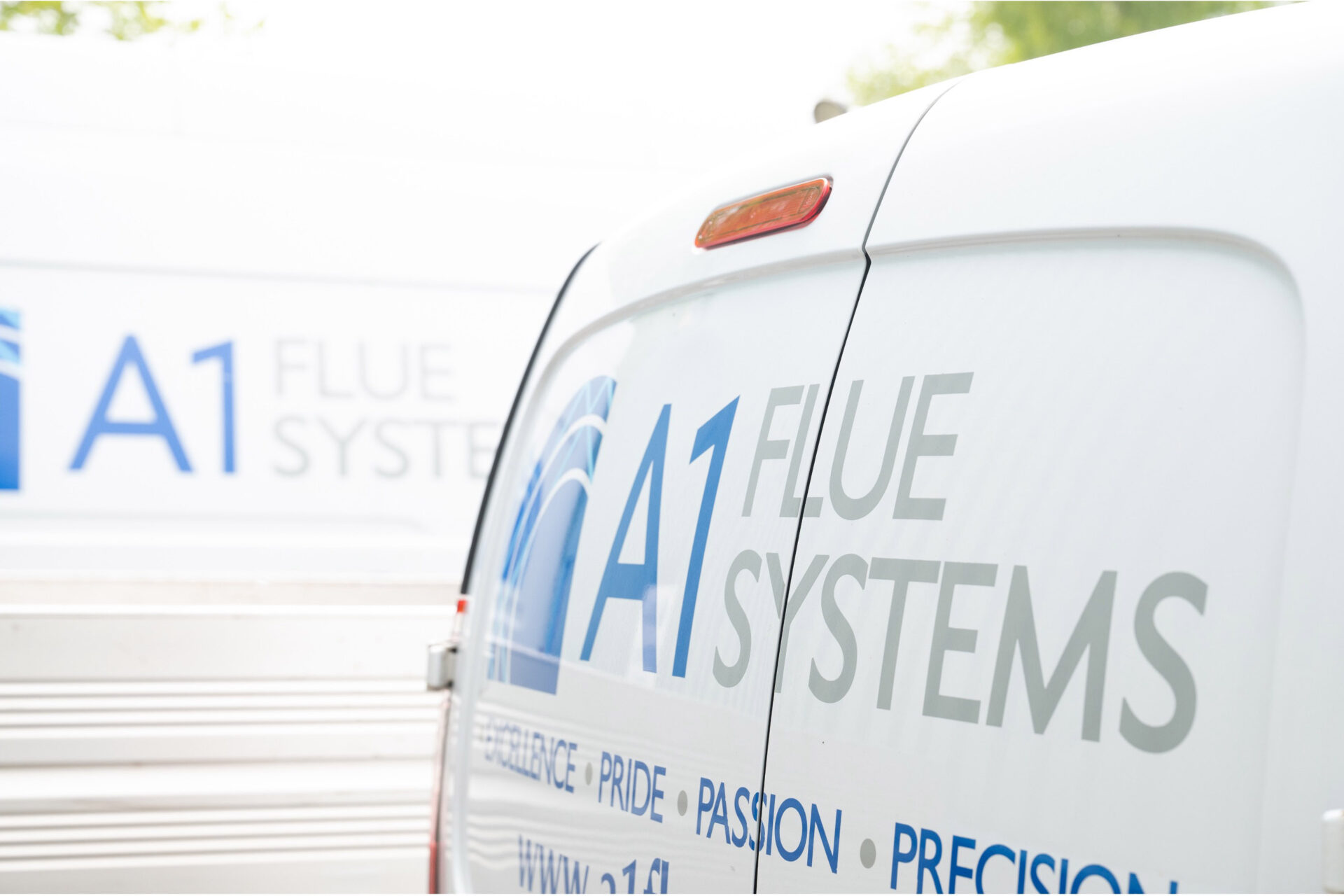
1. Coordination for Efficient Transportation
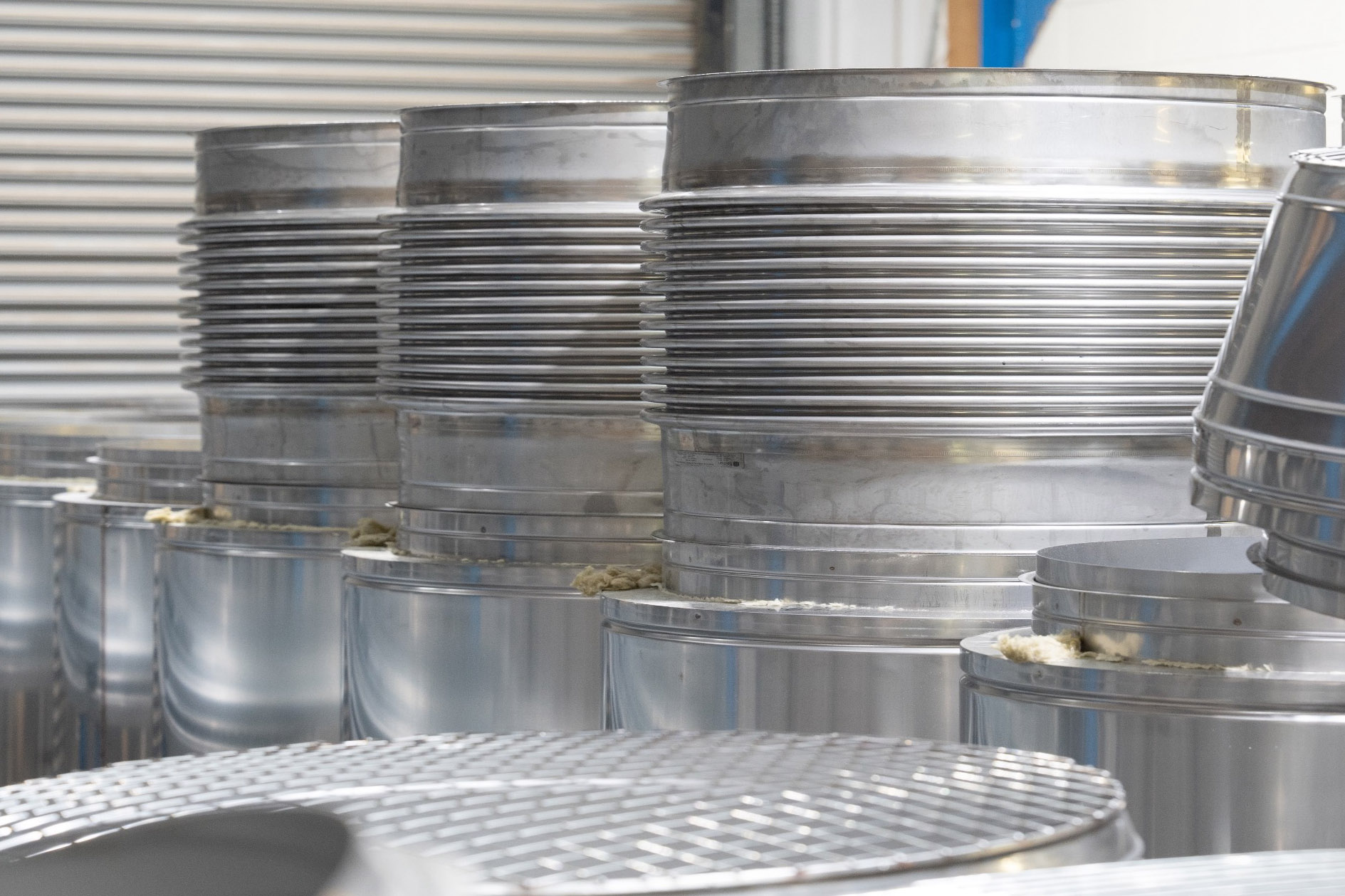
2. Optimization of Inventory Management
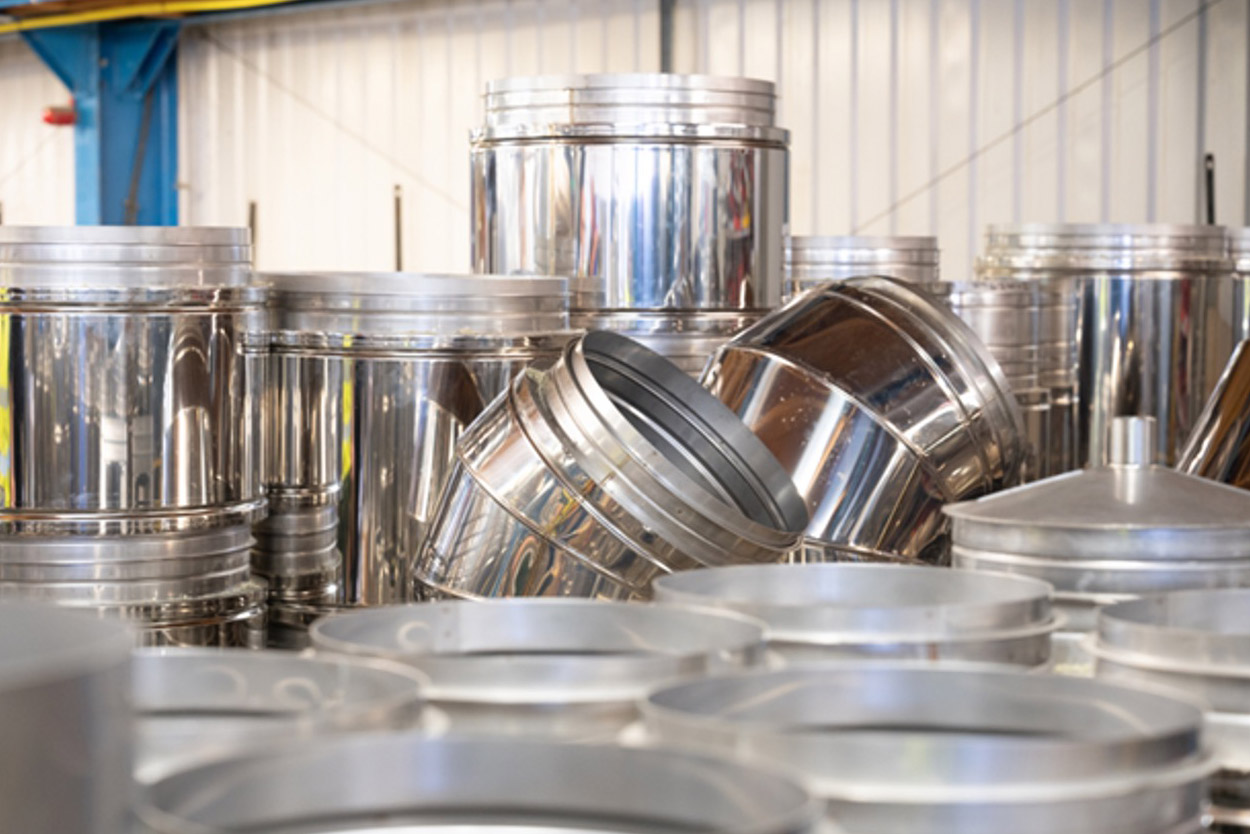
3. Planning and Scheduling for Installation
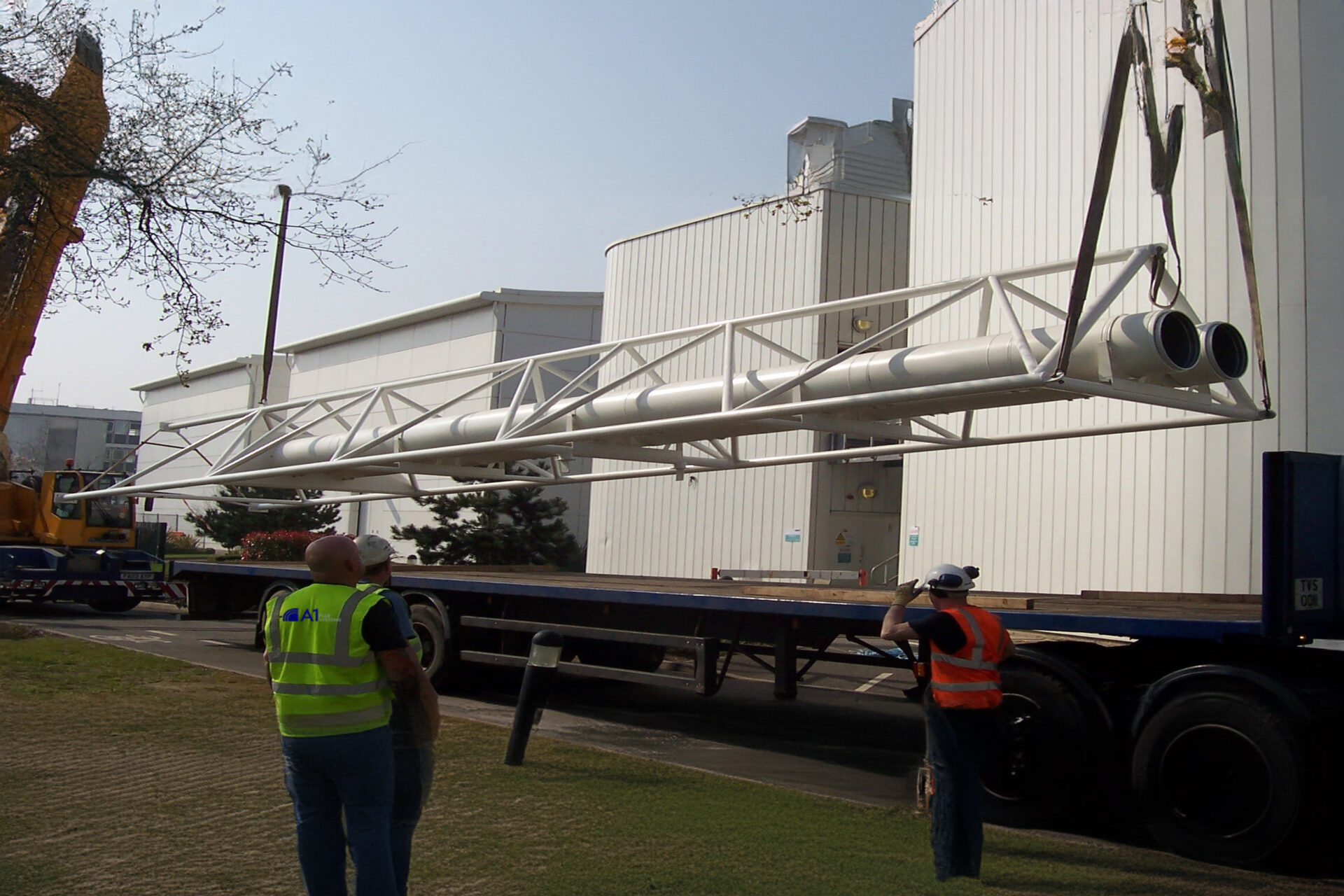
4. Provision of Training and Support Services
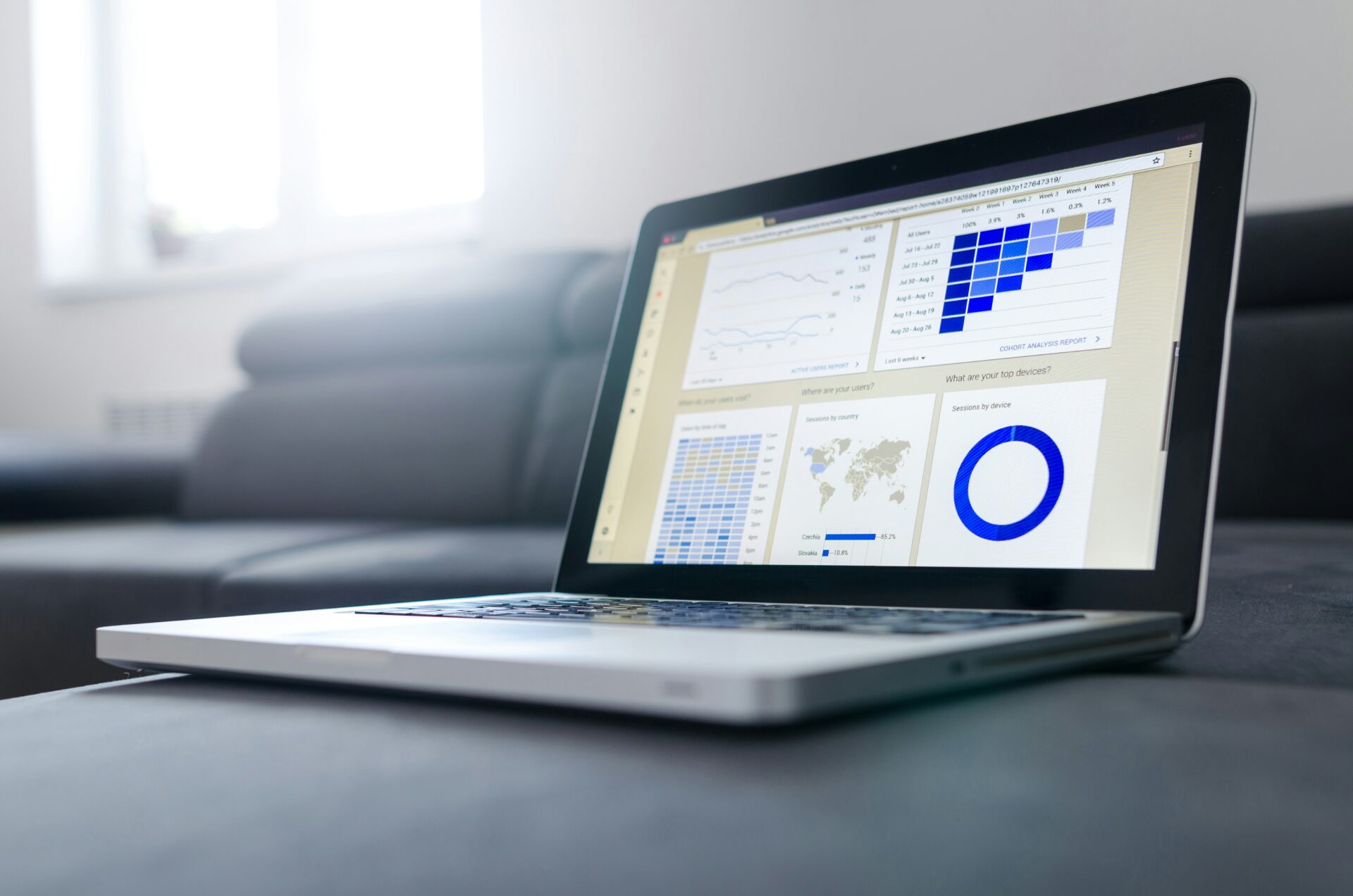
5. Continuous Improvement Initiatives
1. Coordination for Efficient Transportation
Effective communication and coordination between production teams, transport control personnel, and customers are paramount to facilitate the smooth transportation of flue components.
This involves organizing the scheduling of shipments, arranging appropriate transportation modes (such as trucks or freight carriers) and ensuring timely delivery to distribution centers or directly to job sites. By maintaining open channels of communication and collaboration, any logistical challenges can be swiftly addressed, ensuring the efficient flow of materials.
2. Optimization of Inventory Management
Close coordination and implementation of just-in-time (JIT) inventory practices are essential for streamlining inventory management processes.
JIT practices involve maintaining minimal inventory levels and replenishing stock only as needed, thereby reducing storage costs and minimizing the risk of excess inventory. By closely monitoring inventory levels and demand forecasts, logistics professionals can ensure that flue components are readily available when required, optimizing operational efficiency and minimizing lead times.
3. Planning and Scheduling for Installation
Careful planning and scheduling with clients, contractors, architects and project managers are essential to prevent delays and disruptions during the installation phase.
This involves coordinating the delivery of flue components with other construction activities, ensuring that installation occurs at the appropriate stage of the project timeline. By aligning logistical schedules with project milestones and deadlines, potential conflicts can be mitigated, enabling smooth and efficient installation processes.
4. Provision of Training and Support Services
To ensure the safe and efficient execution of installation tasks, logistics providers may offer training and support services to operatives involved in the process.
This includes providing comprehensive training on handling and installing flue components, as well as offering technical support and guidance as needed. By equipping operatives with the necessary knowledge and tools, logistics providers can enhance operational efficiency, minimize errors and promote workplace safety.
5. Continuous Improvement Initiatives
Continuous feedback mechanisms, analysis, and improvement initiatives are integral to optimizing logistics operations and meeting evolving customer demands.
By soliciting feedback from stakeholders, analyzing performance metrics and identifying areas for improvement, logistics providers can implement targeted strategies to enhance efficiency, quality and customer satisfaction. This iterative approach fosters a culture of continuous improvement, enabling logistics operations to adapt and evolve in response to changing market dynamics and customer needs.
Need a Flue?
We'll Help You!