Flue Pipes
Stainless Steel
Flue Pipes
Flue Pipe
Insulation
Flue Pipe
Installation
Broadly speaking, flue pipes fall into two main categories: single-skin flue systems and twin-wall flue systems.
Single-skin flue systems
These stainless steel systems are ideal for both internal and external usage within a commercial property to carry combustion gases away from boilers in CHP units.
All our single-skin flue systems have been successfully tested in accordance with B5476 Part 20 for stability and integrity during a four-hour fire test.
Twin-wall flue systems
These are double lined and contain insulation between the twin walls to reduce the transfer of heat from the interior of the flue to the exterior.
As with the single-skin flues, all our twin-wall flue systems are tested in accordance with B5476 Part 20 for stability and integrity during a four-hour fire test.
Lorem Ipsum
Lorem ipsum dolor sit amet, consectetur adipiscing elit. Morbi id orci sed libero suscipit blandit ut et erat. Ut cursus nisi nunc, hendrerit tempor nisi pharetra in. Fusce enim ligula, fermentum sit amet aliquam eu, volutpat a sem. Quisque laoreet nec urna ut scelerisque.
Lorem Ipsum
Lorem ipsum dolor sit amet, consectetur adipiscing elit. Morbi id orci sed libero suscipit blandit ut et erat. Ut cursus nisi nunc, hendrerit tempor nisi pharetra in. Fusce enim ligula, fermentum sit amet aliquam eu, volutpat a sem. Quisque laoreet nec urna ut scelerisque.
Stainless Steel Flue Pipes
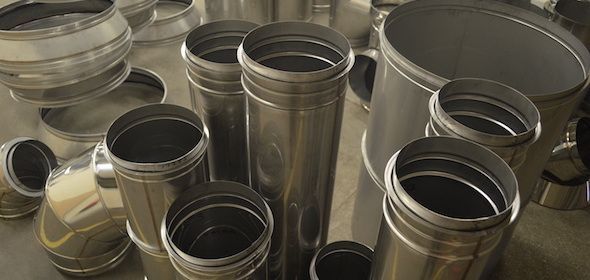
Our stainless steel flue pipes are unparalleled in the construction industry.
That’s because we have a reputation to uphold for the quality, durability and performance of our flue systems, which are used in projects as diverse as skyscrapers such as The Shard in London to train stations in Birmingham.
There are two main kinds of commercial flue and chimney systems: single-skin flue systems and twin-wall flue systems. The choice of which one to use is all down to the requirements of the installation.
Our manufacturing process and the products we produce conform to the requirements of the CE Mark, which became mandatory in July 2013.
Best of British.
As a company that prides itself on being a UK manufacturer, we are equally passionate about ensuring that we have a UK supply chain that can provide all our raw materials – including the stainless steel used to make our flue pipes.
At our 54,000 sq. ft. premises in Nottinghamshire, we have an array of machinery (much of it bespoke to our particular needs) that cuts, turns and forms the stainless steel into the flue systems that we are famous for.
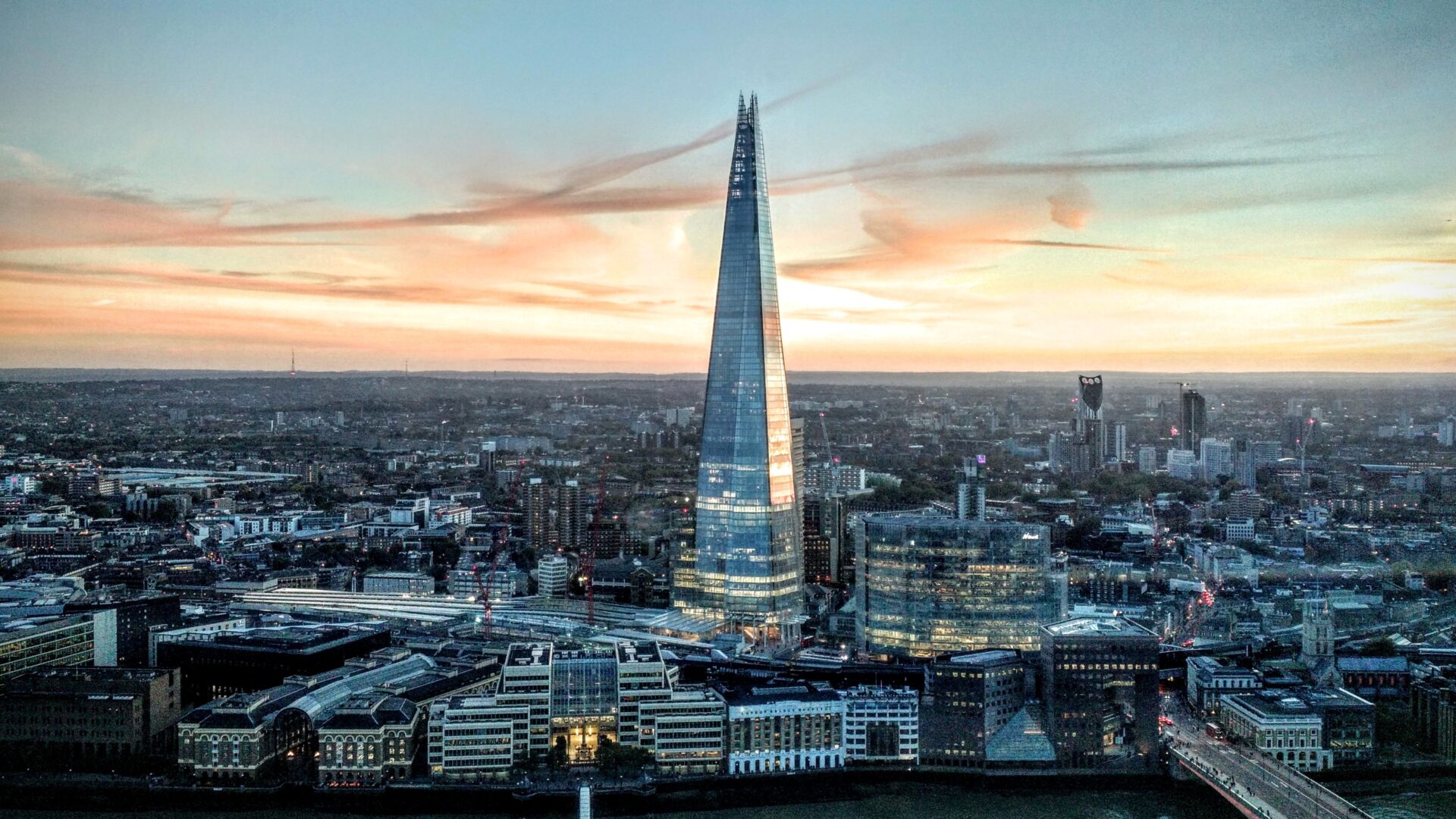
The Shard
READ MORE
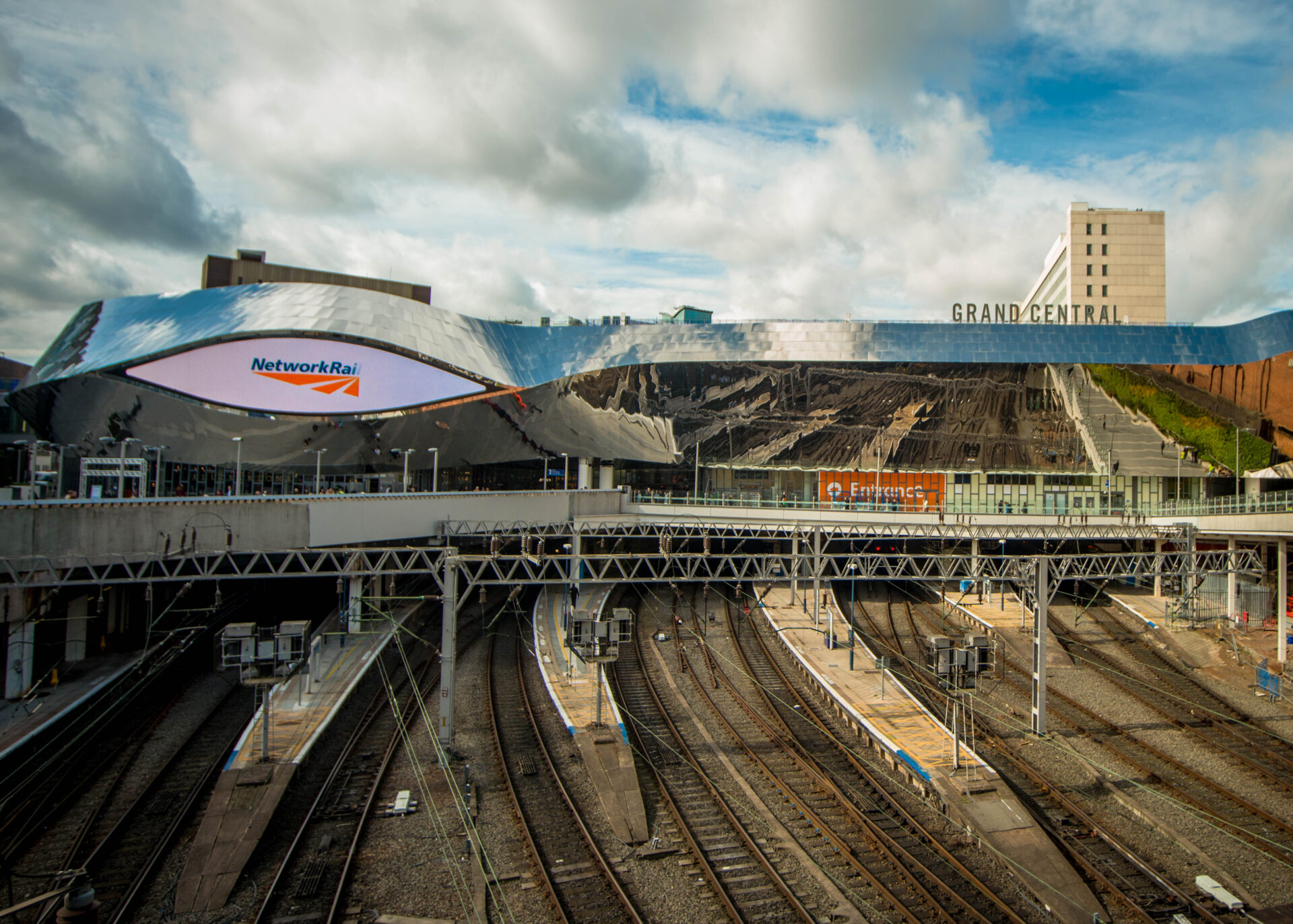
Birmingham New Street Station
READ MORE
Flue Pipe Insulation
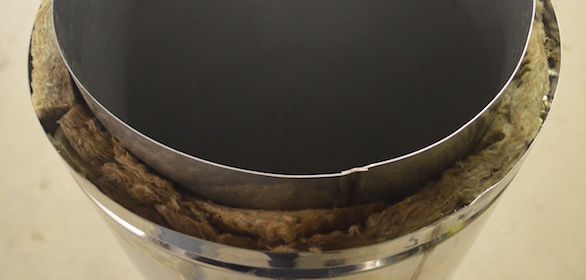
Flue pipe insulation is inserted between the layers of a twin-wall flue system to prevent heat transfer or heat loss as a flue or chimney system takes combustion gases away from boilers and CHP units.
There are two main types of flue pipe insulation: blown and vermiculite.
Blown flue pipe insulation
Blown flue pipe insulation as its names suggests, this type of insulation is blown in the gap between twin-wall flue systems using specialist equipment. It’s a loose, granular material that is very effective at a range of extreme hot and cold temperatures. It is rated as non-combustible in accordance with BS476 Part 4.
Vermiculite flue pipe insulation
When expanded, vermiculite turns into worm-like, accordion-shaped pieces. It is ideal for use as flue pipe insulation because it’s a lightweight, fire-resistant, absorbent and odourless material and is therefore ideal for use as flue pipe insulation.
Blown Flue Pipe Insulation
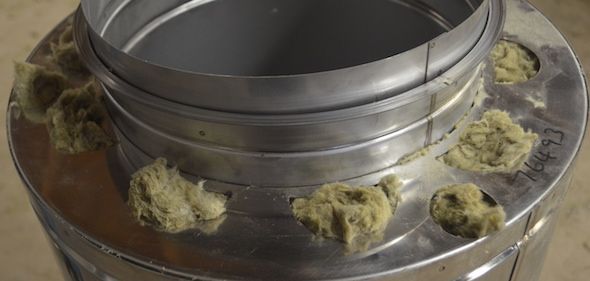
Blown flue pipe insulation is made up of loose, granular material that is either installed by hand or, more commonly, blown into voids using specialist equipment.
This is therefore why most people within the commercial flue systems industry refer to it as blown flue pipe insulation.
It is rated as non-combustible in accordance with BS476 Part 4.
This type of flue pipe insulation is specifically designed for use as an insulation that is in-filled around equipment, within voids and in restricted areas. Its ability to be handled makes it very easy to work with at a range of extreme temperatures, from cryogenic applications all the way through to high-temperature applications.
Effective high-temperature use is dependent upon the installed density. It is recommended that handfill be installed to a density of 150kg/m3 or greater for use at temperatures of up to 800°C. The typical installed density is in the range 45 to 200kg/m3. Our Technical Department can advise on installations where temperatures range from 800°C up to 1500°C.
The advantages of blown flue pipe insulation include:
- It has excellent thermal and acoustic properties
- It is chemically inert and non-combustible
- It is non-hygroscopic
- It has a uniform, granular texture
- It is very simple to install
- It eliminates any gaps
- It is stable and highly versatile
- It is a reliable and cost-effective solution
Vermiculite Flue Pipe Insulation
Vermiculite is a naturally occurring mineral that is ideal for use as flue pipe insulation.
It is usually hand-filled into twin-wall flue systems and in-filled around equipment, within voids and in restricted areas.
It has the unusual property of expanding into worm-like, accordion-shaped pieces when heated.
The expanded vermiculite is a lightweight, fire-resistant, absorbent and odourless material and is therefore ideal for use as flue pipe insulation.
On being suddenly subjected to high temperatures (700°C to 1000°C), vermiculite flakes will expand to many times their original size due to the microscopic layers of water turning to steam and forcing the laminar layers apart.
The properties of vermiculite flue pipe insulation include:
- Sintering temp: 1,260°C %SiO2 46.0
- Melting point: 1,330°C %TiO2 1.0
- Specific gravity: 2.5 %Al2O3 9.8
- Thermal conductivity (k-value): 0.063 W/mK %MgO 27.5
- Specific heat: 1.8 kJ/kg.K %CaO 2.5
- Cation-exchange capacity: 60 milli-equiv / 100g %K2O 2.8
- Sintering temperature: 1,260°C
Flue Pipe Installation
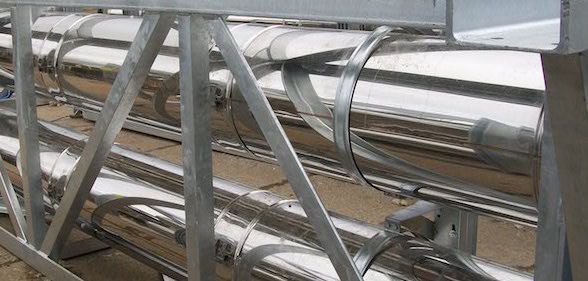
We have used our most popular Deltavent twin-wall flue systems to give a simplified step-by-step guide to flue pipe installation.
Before installation
It is essential that the components are installed with the male spigot down against the flow of gases for all vertical applications. This will allow condensates, if any, to remain within the flue
Important Notes
Nothing should pierce either the internal liner or the outer case at any point of the installation. If Deltavent is exposed to external elements (e.g. rain or snow), it is essential to apply a bead of sealant to the grooves underneath the band.
Flue pipe installation.
- Step 1 – Remove any dirt, grease and other contaminants from components where the sealant will be applied
- Step 2 – Apply an adequate amount of sealant to the male flange connection. Using the locating spigot of the male as a guide, simply push/slot the two parts of the Deltavent twin-wall flue system together (so the male spigot runs down)
- Step 3 – Fit the v-band. This has been designed as a two-piece item for easy assembly and must also be free from any contaminants (e.g. grease or oil)
- Step 4 – Apply sealant into the groove of the v-band before fitting
- Step 5 – Position both v-band parts around the Deltavent with the 10mm connection flange located within the groove
- Step 6 – Tightly fasten both joints using the stainless steel nuts and bolts
Need a Flue?
We'll Help You!